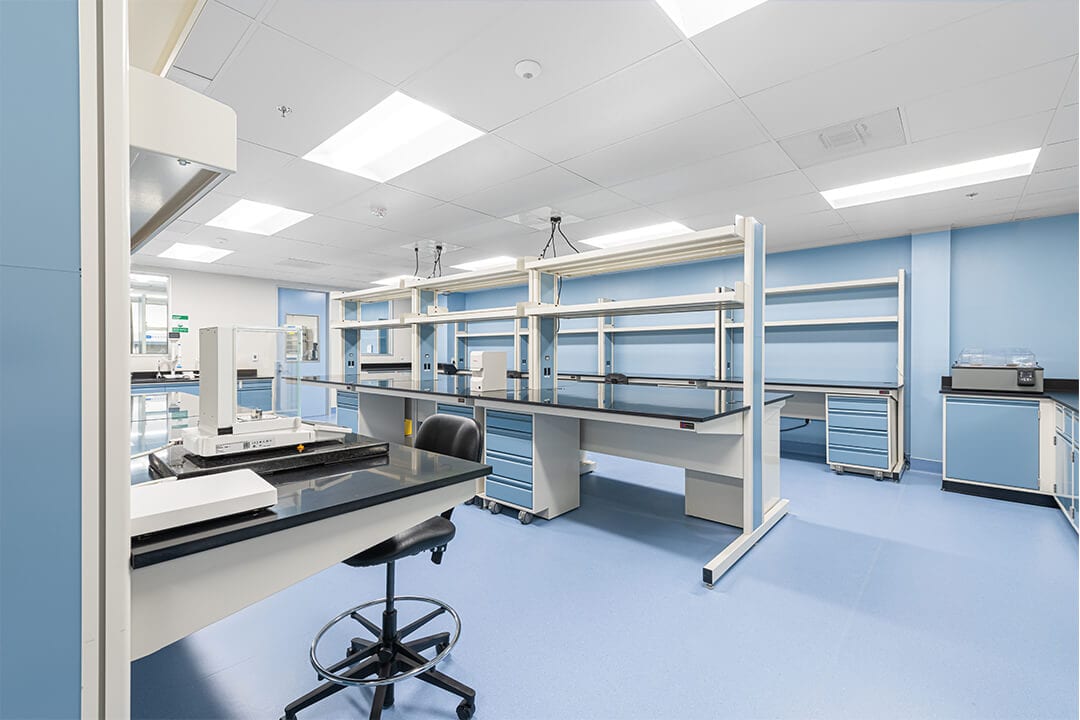
LCS expanded an entire floor dedicated to developing treatments for cancer and autoimmune disorders.
We always say that our clients do great things, and this protein engineering company is no exception. After recently completing Xencor’s 2nd-floor renovation project, we welcomed the opportunity to work with them again to expand their biopharmaceutical operations to the 3rd floor of their Monrovia, California facility.
Xencor develops engineered monoclonal antibodies to treat patients with cancer and autoimmune diseases. A critical component of their work means having a well-established and compliant space that meets regulatory requirements and has the essential equipment for their important product candidates.
Like many of our projects, this renovation took place in an occupied and operational facility. Xencor is a fast-paced company that is reliant upon maintaining workflows for dozens of ongoing research programs at various stages of development, characterization, and preclinical testing. Keeping Xencor operational while avoiding interference to their operations, and properly coordinating multiple trades and construction activities was critical to project success. These challenges required significant planning for logistics, coordination, and scheduling essential installations for the lab furniture, and lifting the cold room condensing units and exhaust fans to the roof.
Developing a site logistics plan to manage project equipment, materials, deliveries, and staging during construction took some creativity and flexibility. We scheduled start times at 5:00 am with early finishes, conducted disruptive activities during off-hours and weekends, and arranged just in time deliveries for equipment and materials.
Construction activities kicked-off with demolition to prepare the space for the improvements. The project included installing mechanical, electrical, and plumbing (MEP) systems, fire sprinklers, fire and life safety systems, lab furniture, cold condensing units, and new interior finishes.
Throughout the project, we managed site safety, site logistics, project schedule, and budget, and adhered to all codes and regulations while preventing impact on facility operations. We maintained responsibility for the integrated project schedule and projected lead times for lab furniture delivery and condensing units and just-in-time deliveries for other equipment and materials.
We worked closely with Xencor’s project team to ensure proper project execution and support for commissioning and construction documentation for GMP certification. We also worked with the lab furniture and condensing unit suppliers to assure adequate equipment and materials integration.
The renovation features office space, a conference room, and multiple R&D and GxP lab areas to expand lab operations. The new space meets Xencor’s environmental laboratory conditions and process requirements for production and supports their facility equipment. The LCS team kept Xencor operational during construction during the expansion of their operations.
We were fortunate that Xencor’s team provided a realistic date for the goal of operation start-up allowing leeway for unforeseen delays such as permitting. After further project assessment, we proposed an earlier project start date and earlier completion date and delivered the project by the goal for operations.
Working with Xencor on several projects since 2011 provides us the opportunity to understand their operations and long-term business goals better and develop a deeper understanding of their cost, quality, and service requirements. It also allows our team to develop a familiarity with their facility and its operations. We understand what it takes to renovate an occupied manufacturing facility successfully. Xencor leveraged LCS’s services to support their higher business goals.